Rozhovory
Automatizace a robotizace zvyšují v Edwards produktivitu výroby
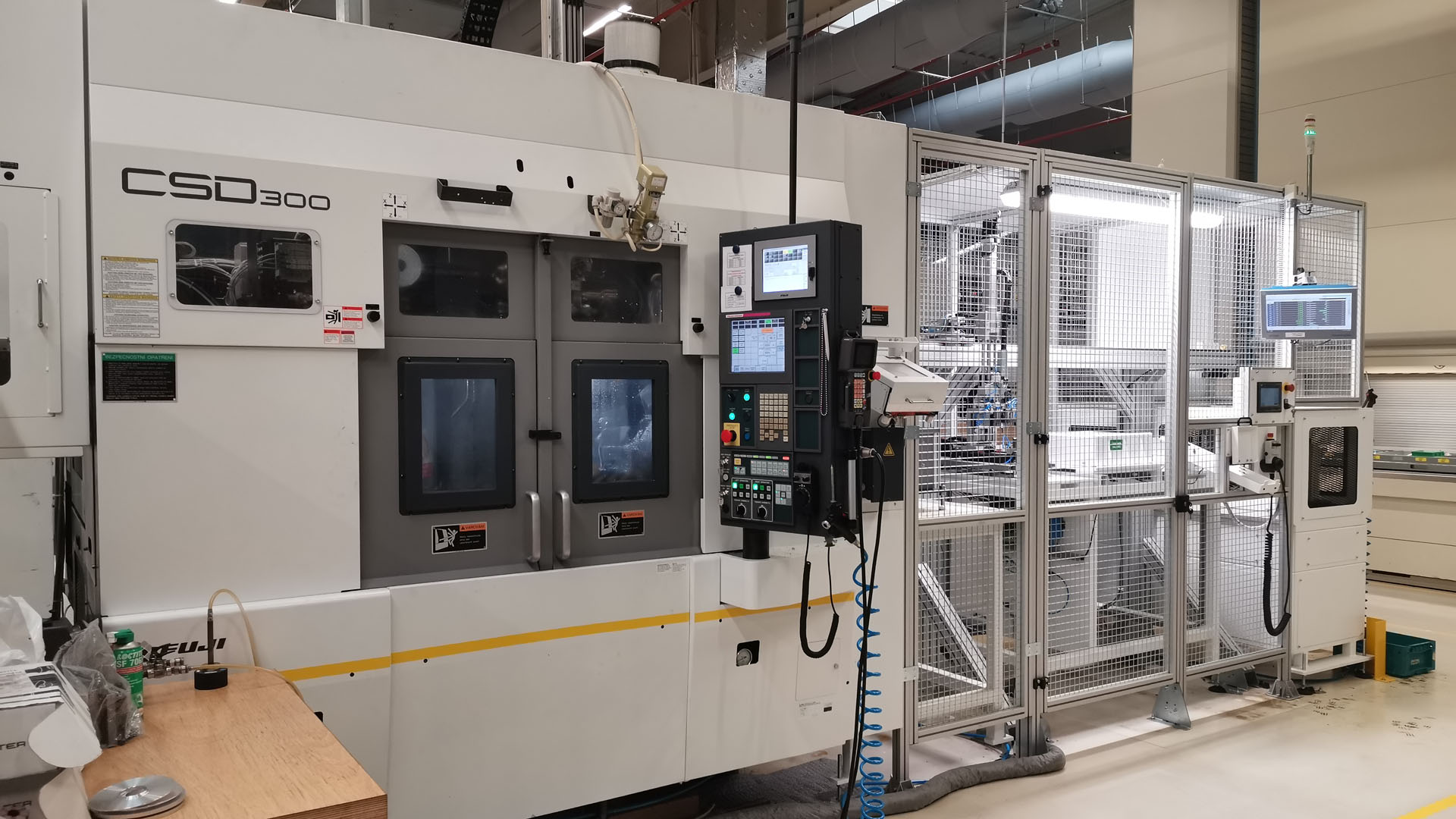
V druhém čísle Reportáží z průmyslu jsme psali o navyšování výrobních kapacit lutínského závodu a s tím související potřebou investic do růstu a obnovy strojového parku. Jak se na něm podílí oddělení technické přípravy výroby?
MH: Oddělení technické přípravy výroby má na starosti zavádění nových produktů do sériové výroby. I když téma obnovy strojového parku patří spíše do oblasti procesního inženýrství, jsem rád, že jsme strategii růstu a obnovy strojů mohli zpracovat v rámci našeho týmu. Zejména proto, že jeho členové mají dlouholeté zkušenosti s našimi procesy a nákupem a testováním nových technologií a jejich know-how bylo pro tvorbu strategie klíčové. Jsem také odpovědný za údržbu a plánování investic do údržby a i v tomto případě došlo k velmi dobrému provázání zkušeností a schopností v celém mém týmu a nasměrování na společný cíl. Na řešení jsme úzce spolupracovali s výrobou, konkrétně s oddělením procesního inženýrství. To mě velmi těší, protože vektoring neboli sladění sil napříč odděleními je jedním z dlouhodobých témat, na která se při řízení závodu zaměřujeme.
Jak jste tedy ke zpracování strategie obnovy přistoupili?
MH: Jde o velmi široké téma a jen zpracování základního hrubého plánu nám zabralo skoro půl roku. Pro představu rozsáhlosti projektu – museli jsme revidovat kategorizaci jednotlivých technologií z pohledu údržby jak na obrobně, tak montáži, následně prioritizovat kroky obnovy více než čtyř desítek strojů v následujících pěti letech, zvážit lidské kapacity, návaznosti jednotlivých výměn, provázanost s růstem výroby a nákupem dalších nových technologií, prostorové možnosti, investiční proces na následujících pět let i způsob komunikace vůči divizi a mateřské společnosti Atlas Copco, protože tyto investice se ve schvalovacím procesu dostanou až na tuto úroveň. S obnovou jednotlivých technologií pak přímo souvisí i zvýšení efektivity při jejich výměně za modernější, například lze několik starých strojů nahradit jedním novým.
Máte nějaký příklad z poslední doby, kdy se vám podařilo při obnově technologií navýšit efektivitu výroby?
Takovým příkladem je obnova technologií, kterou jsme spustili již v roce 2020, a investice byla rozdělena do dvou částí. Hlavním záměrem bylo udržení kapacity výroby, kterou negativně ovlivňovalo stáří a celková kondice strojů, museli jsme řešit jejich poruchovost. Všechny stroje už měly kolem 25 let, a výrazně tak ovlivňovaly průměrné stáří celého strojového parku, které chceme mít výrazně nižší.
V prvním kroku jsme naplánovali výměnu dvou soustruhů. Po analýze výrobního toku a s uvážením vyšší efektivity nové technologie jsme přistoupili ke spojení a automatizaci několika procesů. Dva staré stroje jsme nahradili jedním novým a zároveň jsme stroji předřadili automatický zásobník na polotovary a přímo za stroj jsme instalovali plně automatizovanou měřicí stanici, která stoprocentně kontroluje rozměry jednotlivých obrobků. Tím jsme dosáhli velmi zajímavého zefektivnění celého procesu. Tato technologie je ve výrobě zprovozněna už od podzimu 2021 a po odladění počátečních problémů potvrzuje očekávání. V číslech to znamená, že jsme redukovali obráběcí čas o neuvěřitelných 73,7 procenta. Nová technologie, i když nahradila dva stroje, má o 20 procent vyšší počet vyrobených kusů a s plným zásobníkem polotovarů je schopná samostatně fungovat osm hodin.
Jak jste postupovali v druhém kroku investice?
MH: Investiční záměr pro druhý krok byl schválen v roce 2021. Plánovali jsme dokoupit pětiosé frézovací centrum s vysokootáčkovým vřetenem a opět proces zefektivnit připojením automatizace s robotem. V tomto případě jsme se u automatizace rozhodli pro hotové řešení, a to zejména díky jeho univerzálnosti. Umožňuje snadný přesun automatizace k jakémukoliv jinému stroji, snadné přeprogramování a pro odběr polotovarů a hotových kusů můžeme využít buď vestavěný karuselový zásobník, nebo paletové místo.
Nové pětiosé obráběcí centrum máme v provozu od léta 2022 a letos na podzim bude dodána zmíněná automatizace. Kromě výše uvedených přínosů nám nově instalovaná automatizace umožní nepřetržitou výrobu bez zásahu operátora po dobu až 24 hodin. V obou případech se tedy vyšší efektivita projeví i na snížení zátěže operátorů a lepším využití jejich pracovní doby tak, aby nemuseli přebíhat mezi jednotlivými stroji v rámci přidělené výrobní zóny.
Předpokládám, že takovéto investice mají pozitivní dopady na produktivitu a náklady, je tomu tak?
MB: Zcela určitě. V dnešním dynamickém světě je zvyšování produktivity a snižování nákladů nezbytným předpokladem úspěchu. Modernizace a optimalizace strojového parku jsou jedněmi z klíčových nástrojů, který nám v pomáhá těchto cílů dosáhnout.
Zkrácení výrobního času a optimalizace využití zdrojů jsou totiž hlavními faktory, které ovlivňují produktivitu. Moderní stroje jsou vybaveny pokročilými technologiemi, které umožňují rychlejší výrobu a minimalizaci chyb. Díky investicím do technologických vylepšení můžeme zkrátit dobu potřebnou k výrobě produktu, což vede k většímu výstupu výroby za stejný časový úsek. Můžeme tak uspokojit rostoucí poptávku po našich produktech a zároveň optimalizovat využití pracovních sil, materiálů a energií.
Jak konkrétně se to tedy projevilo v investicích, které jste zmínili výše?
MB: V případě nahrazení zastaralých soustruhů novou technologií se podařilo snížit zpracovací náklady o 13 procent u produktu, který je z pohledu objemu výroby významný. Díky tomu jsme dosáhli velmi zajímavé návratnosti investice. Úspory se projevily nejen v mzdových nákladech a nákladech na energie, ale také díky vyšší spolehlivosti a sníženým poruchám v nákladech na opravy a údržbu. Pětiosé frézovací centrum nám umožnilo navýšit technické kapacity, tím zareagovat na zvýšenou poptávku po našich produktech, a využít tak potenciálu úspor z rozsahu. Další pozitivní přínos pak očekáváme z již zmíněné automatizace.
Velmi důležitá oblast, kterou nesmíme opomenout, je vliv investice na životní prostředí, který při vyhodnocování vždy posuzujeme. Volba udržitelných technologií a energeticky efektivních zařízení nám přináší nejen úspory nákladů, ale pomáhá také omezit negativní dopady na životní prostředí. A to je téma, které aktuálně rezonuje společností a stále více ovlivňuje preference zákazníků.
Jaké máte plány do budoucna?
MB: Zmíněné příklady jasně ilustrují, že přínos investice ve formě zvýšené produktivity, zkrácení výrobních časů, menší spotřeby zdrojů, úspory nákladů na údržbu strojového parku a minimalizace dopadů na životní prostředí vytvářejí synergický efekt, který zlepšuje naši konkurenceschopnost a vytváří předpoklady pro dlouhodobý úspěch podniku. Plán obnovy strojového parku máme připraven a odsouhlasen naší mateřskou společností. V následujících letech budeme investovat desítky milionů korun do nových technologií, abychom naplnili naši vizi stát se nejlepším závodem vakuové techniky, který dodává vakuové vývěvy do celého světa.